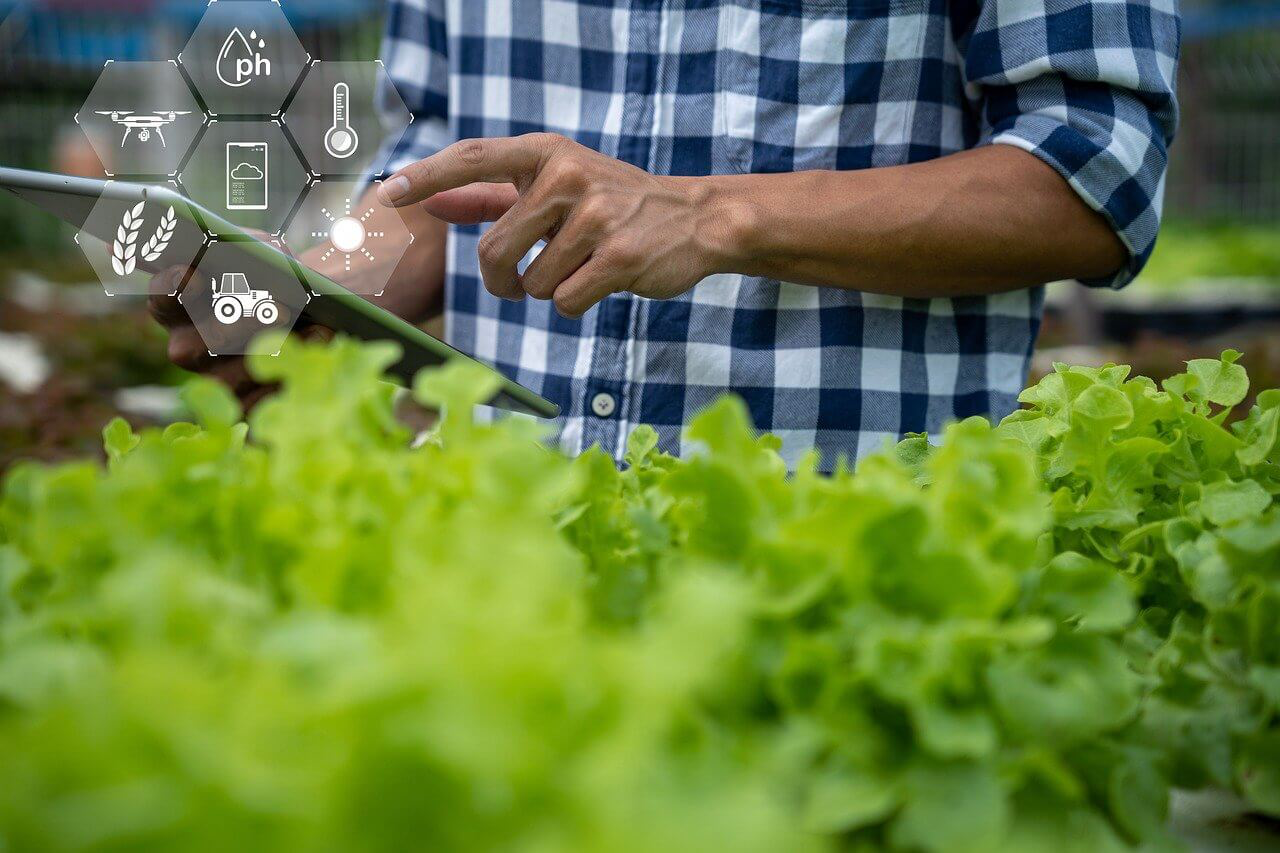
Farming systems involving collaboration between humans and robots offer a route to simplifying and reducing the cost of rolling out ‘Agriculture 4.0’ technologies, according to a collaborative piece of research from agricultural and industrial engineering experts.
In the paper by George Adamides and Yael Edan, the researchers suggest that the complex and unstructured nature of the agricultural environment, including unpredictable terrain, varied climatic conditions and the need to handle biological materials, is currently limiting the performance of autonomous technologies.
Human-robot collaboration (HRC) could be the key to improving outcomes, they wrote, while offering the opportunity to work in a high-tech environment could also help in recruiting younger people to the agricultural profession.
Few studies to date
Adamides and Edan reviewed research to date on HRC, finding a relatively small number of examples, with much of the work focused on harvesting, spraying and navigating. Safety, usability and functionality have been the primary interests of academics, and in particular, the key role that humans can play in planning effective navigation of robots, as well as specifying and verifying how a robot interacts with the environment.
“When we humans think of robots, we often associate them with autonomous actions. So, the primary effort is to work towards making them fully autonomous and as a result, the research interest to human-robot collaboration is not as high as one would expect,” said Adamides, from the Agricultural Research Institute in Cyprus.
Steps on the road to ‘smart farming’
HRC systems could serve as intermediate steps towards autonomy, helping to overcome bottlenecks in the development of fully autonomous systems, the authors wrote in the journal Computers and Electronics in Agriculture.
As an example, they suggested that designing an automated system to harvest 100% of fruit grown would be difficult and expensive, whereas a system that aimed to harvest 70%, with humans harvesting the remainder, would be simpler and cheaper.
The researchers pointed to real-world case studies that illustrate successful collaboration. These included improved harvesting of avocados in Chile and planning for selective pepper harvesting using robotics to assess pepper maturity.
Assisting a shift in focus
With research gaps still remaining, they went on to provide a series of suggestions for future work. These include more clearly defining the robot and human needs for specific tasks, enhanced safety features, and interfaces that allow non-experts to operate both autonomous and manual equipment on farm sites.
As yet, there are no legal frameworks in place for either or autonomous or collaborative systems, they noted, but it is to be expected that humans will need to remain ‘in the loop’ for safety and liability reasons, with clear standards needed for human responsibilities in these new relationships.
“We’re trying to bring a change in mindset,” added Edan, from Ben-Gurion University of the Negev in Israel.
“Since humans will be around in agriculture anyway, for the ‘green thumb’, improved decision making, and that fact that many tasks that can’t be automated, we should use them.”