Written by CPM Magazine from CPM Magazine
Download PDF
On a recent visit to India, CPM finds out more about its farming and how BKT, who hosted the tour, is investing heavily in its growing global business and range of tyres and tracks.
By Martin Rickatson
The world’s seventh largest land area – almost 3.3 million km2 – and second highest population, at 1.3bn, have helped India become the second biggest global producer of both wheat and rice.
And it isn’t only its second-place global ranking for production of the world’s two most widely-grown grains that puts India near the top of food producing nations. The country is also the world’s largest producer of pulses and milk, and ranks second for cotton, sugarcane, vegetables and fruit.
But while it may be more than 4500 miles from the UK, India’s influence is being felt more and more keenly. India supplies 12.5% – one-eighth – of the world’s wheat, so has a big influence on the global grains sector which has a direct impact on the factors which influence the UK grain trade.
In recent years, India has increasingly satisfied national demand and become a more prominent exporter, now ranking 10th in the world for wheat as exports having rocketed by 609% between 2020 and 2021. In addition, the country is the globe’s largest producer and consumer of pulses, each figure representing around 25%, as well as being a significant importer.
The nation’s economy is also not be sniffed at. It boasts the world’s sixth largest by GDP, and with 20% of that accounted for by agriculture – which employs 45% of the workforce – farming is of considerable overall significance. Yet it faces considerable challenges.
Over three-quarters of farms are classed as small and marginal, making mechanisation difficult and costly, while there are pressures on water resources, and significant hunger and malnourishment. In addition, a rising population and greater urbanisation are potentially creating problems for the future.
At Surat, near Gujarat, Rajdeep Patel has eliminated artificial crop protection and fertiliser inputs with mulch applications and has adopted an intercropping system.
But key productivity indicators, including cropping intensity, yields, horsepower/ha and levels of mechanisation have all been increasing in recent decades. Machinery is becoming more widely adopted, with tractors used as more than simple transporters. And farmers are facing their challenges with some ideas that, in principle, bear comparison with those being adopted in certain UK farming practices.
At Surat, near Gujarat, close to the Pakistan border on the north-west coast, BKT hosted a group of European journalists on a visit a small-scale vegetable farm run by Rajdeep Patel. He’s not only co-operating in key areas with neighbouring farmers, he’s eliminated artificial crop protection and fertiliser inputs with mulch applications and has also adopted an intercropping system, principles now attracting interest on some UK farms.
Rajdeep’s unit extends to just two hectares – although this is around double the average size for an Indian farm – but grows 60 different crops throughout the year, many of them planted alternately within the same rows and varying considerably in height and in rooting depth.
He follows principles established by Indian farm adviser Subhash Palekar, which includes replacing purchased inputs with those sourced closer to home. As 1.5-2.0 % of required nutrients are taken from the soil by the plant – with the remainder from air, water and solar energy – inorganic fertilisers are calculated to be unnecessary. Home-saved seed and natural crop protection products are an extension of this philosophy.
The second principle indicates that locked-up cations – nitrogen, phosphate, potash, iron, sulphur and calcium – present in the soil can be made accessible through the action of micro-organisms. These, including bacteria, microbes and earthworms, can be reintroduced and encouraged through manure application.
One cow is reckoned to produce around 10kg of dung daily, sufficient for the monthly fertiliser needs. This is bolstered by a natural catalytic agent called jivamrit, produced to promote humus formation by encouraging the multiplication of micro-organisms that decompose dried biomass, breaking it down into plant-accessible nutrients.
Similarly, a liquid seed treatment, bijamrita – a mixture of water, cow dung and urine, soil and lime – is said to have proven successful at minimising seed-borne disease development. Other natural fungus and insect inhibitors are made using blends of crushed tobacco, green chilli, garlic, neem, and fruits including custard apple, guava, Lantena camella, papaya, white dhotara and pomegranate.
Mulching is the third principle, deemed necessary to create the micro-climate in which micro-organisms can best develop, at 25-32C and 65-72% moisture.
Lastly, intercropping, multicropping or mixed cropping are advocated to promote beneficial plant interaction. Key ideas include mixing long lifespan species – including trees such as coconut and mango – with short life ones, such as vegetables and medium-term species including banana and papaya. This is reckoned to spread risk, limit potential damage from pest and disease outbreaks, and encourage biodiversity.
Growing crops in layers of height ensures maximum access to light for each layer, and means they also have different rooting depths and masses.
“We grow crops in layers of height, to ensure maximum access to light for each layer,” explained Rajdeep.
“This generally means they also have different rooting depths and masses, again complementing each other within the soil profile, helping keep it open yet retain moisture – which is especially important, not just because of our low rainfall through much of the year, but also because of the salinity issues created by our proximity to the sea.
“My aim, when founding this farm a year ago, was a cropping system that harnessed nature to do the work of retaining nutrients, conserving moisture, maintaining the soil structure and minimising the risk of disease development. And I wanted to eliminate any need for chemical solutions to seed protection and weed, pest and disease control.”
Biological disease suppression and nutrient supply are aided by the use of jivamrit, a water, cow dung and urine, pulse flour, soil and jaggery (sugar cane juice) blend, applied in 500 l/ha of water.
The farm has its own reservoirs and is connected to government-built channels from the nearest river, into which water is released every 15 days.
“One of our key focus areas is on maintaining humus levels to minimise irrigation requirements, and the remaining material helps here, being applied as a nutrient-rich mulch.”
The aim of intercropping is to grow symbiotic crops known to have mutually beneficial effects when planted adjacent to each other. They include species ranging from turmeric and chilli to cauliflower and guava, spaced beneath trees including avocado and papaya. Planting harvest cycles are short for smaller species, and these are replanted rotationally every three months in 36m-by-36m plots.
“With our annual rainfall of 1000-1250mm almost all falling in the July to September rainy season, moisture preservation and rain collection are essential. Plant harvest waste is used as mulch and manure is purchased from local cattle farmers,” he says.
“We have our own reservoirs, the water from which is used with care through the dry season. But we’re also connected to government-built channels from the nearest river, into which water is released every 15 days and from which we can extract water, at cost, when necessary. In a good rainfall year, well-managed water means we can grow good crop yields.”
BKT makes big factory investments
BKT has the Indian ag tyre industry’s only ‘real world’ external test tracks, including tarmac to assess road characteristics, a tarmac/mud/stone combination for durability tests, and an automated track.
Indian tyre manufacturer BKT, which organised the farm tour on the back of a visit to its Bhuj factory, continues to make inroads into the European and global agricultural tyre markets, and revealed plans to further extend its manufacturing footprint.
“While we’re still a relatively new name in the UK and European agricultural tyre markets, and a relatively young business as a whole, BKT has grown rapidly in recent years,” said Rajiv Poddar, joint managing director.
“We turned over $1bn in 2022, and our target is to double that by 2026. We hope much of that will come from organic market growth. BKT is now a well-known name in agriculture tyres and we have invested heavily in marketing to show that we mean business in terms of quality tyre production. But peer-to-peer conversations between satisfied farmers talking to their neighbours have been possibly our best driver of growth and have helped boost the perception of our brand.
“We’re only involved in manufacturing tyres for mostly off-road use, and agriculture has traditionally represented 80 per cent of our business, although with the development of our industrial and forestry tyre interests as we diversify our portfolio, that figure is now around 60%.
“Unlike some other companies, we operate with a single brand, under which we manufacture 3400 types and sizes of tyre.”
One of five BKT industrial tyre factories in India, with others at Aurangabad, Bhiwadi, Chopanki and Dombivli, the Bhuj plant is the company’s newest, and is sited 850km north of Mumbai, on India’s west coast near to the Pakistan border, close to the port of Mundra to minimise export costs.
Construction on the 125ha site began in 2010 and was funded by a $500m investment. Two years after work commenced, the first tyres – solid units for industrial use on concrete – left the production line.
More recent Bhuj developments include a 10ha research and development site, completed in 2017. Among other areas, this includes laboratories for testing carcase and tread designs, and compound formulations and blends. Four simulators allow loads and impacts in different situations to be simulated before concepts are selected for further development.
Physical testing includes tyre rollers/rotators, which operate up to 24 hours a day for as long as 120 hours at a time, producing rotational wear and side load stresses to allow impacts to be assessed. Meanwhile, there are also the Indian agricultural tyre industry’s only ‘real world’ external test tracks, including a long tarmac facility to assess wear characteristics and noise; a tarmac, mud, and stone combination to test durability; and an automated track where tractors can be installed and run driverless to simulate and assess the long-term effects of steering and turning.
Manufacturing on the Bhuj site includes a new radial tyre production facility completed in 2021, boosting company production to 700 tonnes of radial tyres daily, of which the new Bhuj plant represents 436 tonnes. The company manufactures its own tyre moulds, and the use of technology is extensive to maximise the quality of products and working conditions, with robots cutting raw material rubber sheeting to size, and cameras checking production process quality.
Some 40-45 export containers leave the site each day, with tyres drawn from a finished product storage facility that covers 5ha (12.5ac) under a 260m x 190m single roof, able to hold 15 days’ production, or 82,500 tyres weighing 6500 tonnes, to ensure they are protected from weathering before despatch.
In an additional $0.5bn investment, BKT’s presence in Bhuj is now being extended in size by 30% to 323ha, in a move that will enable the firm to not only further increase tyre output but also ramp up production of carbon black, a key ingredient in tyre compounds.
The firm began production of its own carbon black in 2017, being the first tyre maker of its type to do this. BKT now manufactures around 165,000 tonnes annually, and the new operation will extend this to 200,000 tonnes. It’s anticipated the carbon black plant will be operating within two years, producing 600,000 tonnes annually by 2026.
Environmental responsibilities
BKT says it fully recognises its environmental responsibilities as a tyre manufacturer and is addressing them in multiple ways. As an example, Bhuj incorporates its own modern high-efficiency power plant, comprising two 20MW steam turbines, supported by solar panels and wind turbines that generate up to 50 per cent of the factory’s electricity requirements. Approximately 900 families live in a village constructed on-site for staff, and a school is under construction, to minimise workforce impact in an area which was previously sparsely populated.
Natural rubber remains an important tyre ingredient, and the company’s lab work is currently assessing higher levels of natural product integration into tyre manufacture, part of a wider aim to minimise plastic and oil usage. Research is also ongoing into used tyre recycling, a significant challenge given they’re a compound of rubber, synthetic materials and metals.
With the Bhuj plant alone using 4M litres daily, tyre manufacturing is a water-hungry process, and there are large areas of storage on-site for captured rainwater. All used water is treated and recycled via reservoirs on site, stocked with fish to help gauge quality. Almost a third of the site area is planted, and an on-site nursery produces bushes and trees to build on and replenish this.
OEM and replacement track markets
Track production at Bhuj recently began, with current production at 20-25/day of the 18x6x44 units in a pre-production/testing phase.
After building brand awareness in the agricultural tyre market over recent years, BKT has recently branched out into OEM/replacement tracked tractor rubber, with the launch last year of Agriforce BK T71 for high-hp machines.
As with most tyre/track manufacturers, BKT keeps the formula for its rubber compound closely-guarded but describes it as a ‘high performance’ formulation designed to provide strong resistance against cuts, tears and abrasion. Research into the ideal tread is reckoned to have produced an optimised pattern said to maximise traction and ride comfort, while the shape of the positive-drive lugs is claimed to maximise flexibility, and the carcase is made from four ply layers reinforced with high-tensile steel cord.
Track production at Bhuj recently began, with current production of around 20-25/day of the 18x6x44 units in a pre-production/testing phase before deals with OEMs and with suppliers for replacement sales begin. By next year the aim is to increase production 10-fold, for which a dedicated track production facility is being built.
“While track units have been developed initially for use on tractors, the next market to be targeted will be OEM and replacement combine tracks,” said Dilip Vaidya, BKT technical director. “We’re also developing new solid tyres for machine applications on concrete, taking us into other agricultural markets such as uses on compact forklifts for use in vegetable processing plants.
“And we are also working closely with the development of electrically-powered tractors, with the tyre designs necessary to make the most of their capabilities and match their specific needs, such as minimising rolling resistance to maximise battery charge life.”
This article was taken from the latest issue of CPM. For more articles like this, subscribe here.
Sign up for Crop Production Magazine’s FREE e-newsletter here.
The post A taste of India appeared first on cpm magazine.
Continue reading on CPM website...
If you are enjoying what you read then why not considering subscribing here: http://www.cpm-magazine.co.uk/subscribe/
Download PDF
On a recent visit to India, CPM finds out more about its farming and how BKT, who hosted the tour, is investing heavily in its growing global business and range of tyres and tracks.
“Peer-to-peer conversations between satisfied farmers talking to their neighbours have been possibly our best driver of growth.”
By Martin Rickatson
The world’s seventh largest land area – almost 3.3 million km2 – and second highest population, at 1.3bn, have helped India become the second biggest global producer of both wheat and rice.
And it isn’t only its second-place global ranking for production of the world’s two most widely-grown grains that puts India near the top of food producing nations. The country is also the world’s largest producer of pulses and milk, and ranks second for cotton, sugarcane, vegetables and fruit.
But while it may be more than 4500 miles from the UK, India’s influence is being felt more and more keenly. India supplies 12.5% – one-eighth – of the world’s wheat, so has a big influence on the global grains sector which has a direct impact on the factors which influence the UK grain trade.
In recent years, India has increasingly satisfied national demand and become a more prominent exporter, now ranking 10th in the world for wheat as exports having rocketed by 609% between 2020 and 2021. In addition, the country is the globe’s largest producer and consumer of pulses, each figure representing around 25%, as well as being a significant importer.
The nation’s economy is also not be sniffed at. It boasts the world’s sixth largest by GDP, and with 20% of that accounted for by agriculture – which employs 45% of the workforce – farming is of considerable overall significance. Yet it faces considerable challenges.
Over three-quarters of farms are classed as small and marginal, making mechanisation difficult and costly, while there are pressures on water resources, and significant hunger and malnourishment. In addition, a rising population and greater urbanisation are potentially creating problems for the future.
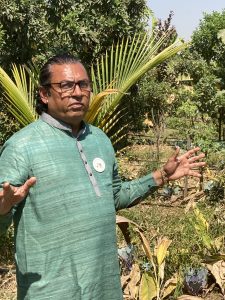
At Surat, near Gujarat, Rajdeep Patel has eliminated artificial crop protection and fertiliser inputs with mulch applications and has adopted an intercropping system.
But key productivity indicators, including cropping intensity, yields, horsepower/ha and levels of mechanisation have all been increasing in recent decades. Machinery is becoming more widely adopted, with tractors used as more than simple transporters. And farmers are facing their challenges with some ideas that, in principle, bear comparison with those being adopted in certain UK farming practices.
At Surat, near Gujarat, close to the Pakistan border on the north-west coast, BKT hosted a group of European journalists on a visit a small-scale vegetable farm run by Rajdeep Patel. He’s not only co-operating in key areas with neighbouring farmers, he’s eliminated artificial crop protection and fertiliser inputs with mulch applications and has also adopted an intercropping system, principles now attracting interest on some UK farms.
Rajdeep’s unit extends to just two hectares – although this is around double the average size for an Indian farm – but grows 60 different crops throughout the year, many of them planted alternately within the same rows and varying considerably in height and in rooting depth.
He follows principles established by Indian farm adviser Subhash Palekar, which includes replacing purchased inputs with those sourced closer to home. As 1.5-2.0 % of required nutrients are taken from the soil by the plant – with the remainder from air, water and solar energy – inorganic fertilisers are calculated to be unnecessary. Home-saved seed and natural crop protection products are an extension of this philosophy.
The second principle indicates that locked-up cations – nitrogen, phosphate, potash, iron, sulphur and calcium – present in the soil can be made accessible through the action of micro-organisms. These, including bacteria, microbes and earthworms, can be reintroduced and encouraged through manure application.
One cow is reckoned to produce around 10kg of dung daily, sufficient for the monthly fertiliser needs. This is bolstered by a natural catalytic agent called jivamrit, produced to promote humus formation by encouraging the multiplication of micro-organisms that decompose dried biomass, breaking it down into plant-accessible nutrients.
Similarly, a liquid seed treatment, bijamrita – a mixture of water, cow dung and urine, soil and lime – is said to have proven successful at minimising seed-borne disease development. Other natural fungus and insect inhibitors are made using blends of crushed tobacco, green chilli, garlic, neem, and fruits including custard apple, guava, Lantena camella, papaya, white dhotara and pomegranate.
Mulching is the third principle, deemed necessary to create the micro-climate in which micro-organisms can best develop, at 25-32C and 65-72% moisture.
Lastly, intercropping, multicropping or mixed cropping are advocated to promote beneficial plant interaction. Key ideas include mixing long lifespan species – including trees such as coconut and mango – with short life ones, such as vegetables and medium-term species including banana and papaya. This is reckoned to spread risk, limit potential damage from pest and disease outbreaks, and encourage biodiversity.
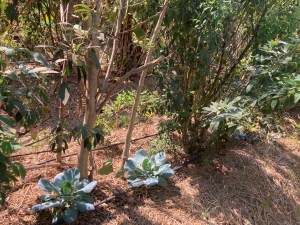
Growing crops in layers of height ensures maximum access to light for each layer, and means they also have different rooting depths and masses.
“We grow crops in layers of height, to ensure maximum access to light for each layer,” explained Rajdeep.
“This generally means they also have different rooting depths and masses, again complementing each other within the soil profile, helping keep it open yet retain moisture – which is especially important, not just because of our low rainfall through much of the year, but also because of the salinity issues created by our proximity to the sea.
“My aim, when founding this farm a year ago, was a cropping system that harnessed nature to do the work of retaining nutrients, conserving moisture, maintaining the soil structure and minimising the risk of disease development. And I wanted to eliminate any need for chemical solutions to seed protection and weed, pest and disease control.”
Biological disease suppression and nutrient supply are aided by the use of jivamrit, a water, cow dung and urine, pulse flour, soil and jaggery (sugar cane juice) blend, applied in 500 l/ha of water.
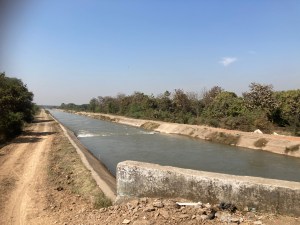
The farm has its own reservoirs and is connected to government-built channels from the nearest river, into which water is released every 15 days.
“One of our key focus areas is on maintaining humus levels to minimise irrigation requirements, and the remaining material helps here, being applied as a nutrient-rich mulch.”
The aim of intercropping is to grow symbiotic crops known to have mutually beneficial effects when planted adjacent to each other. They include species ranging from turmeric and chilli to cauliflower and guava, spaced beneath trees including avocado and papaya. Planting harvest cycles are short for smaller species, and these are replanted rotationally every three months in 36m-by-36m plots.
“With our annual rainfall of 1000-1250mm almost all falling in the July to September rainy season, moisture preservation and rain collection are essential. Plant harvest waste is used as mulch and manure is purchased from local cattle farmers,” he says.
“We have our own reservoirs, the water from which is used with care through the dry season. But we’re also connected to government-built channels from the nearest river, into which water is released every 15 days and from which we can extract water, at cost, when necessary. In a good rainfall year, well-managed water means we can grow good crop yields.”
BKT makes big factory investments
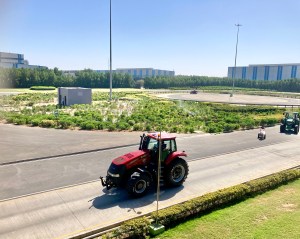
BKT has the Indian ag tyre industry’s only ‘real world’ external test tracks, including tarmac to assess road characteristics, a tarmac/mud/stone combination for durability tests, and an automated track.
Indian tyre manufacturer BKT, which organised the farm tour on the back of a visit to its Bhuj factory, continues to make inroads into the European and global agricultural tyre markets, and revealed plans to further extend its manufacturing footprint.
“While we’re still a relatively new name in the UK and European agricultural tyre markets, and a relatively young business as a whole, BKT has grown rapidly in recent years,” said Rajiv Poddar, joint managing director.
“We turned over $1bn in 2022, and our target is to double that by 2026. We hope much of that will come from organic market growth. BKT is now a well-known name in agriculture tyres and we have invested heavily in marketing to show that we mean business in terms of quality tyre production. But peer-to-peer conversations between satisfied farmers talking to their neighbours have been possibly our best driver of growth and have helped boost the perception of our brand.
“We’re only involved in manufacturing tyres for mostly off-road use, and agriculture has traditionally represented 80 per cent of our business, although with the development of our industrial and forestry tyre interests as we diversify our portfolio, that figure is now around 60%.
“Unlike some other companies, we operate with a single brand, under which we manufacture 3400 types and sizes of tyre.”
One of five BKT industrial tyre factories in India, with others at Aurangabad, Bhiwadi, Chopanki and Dombivli, the Bhuj plant is the company’s newest, and is sited 850km north of Mumbai, on India’s west coast near to the Pakistan border, close to the port of Mundra to minimise export costs.
Construction on the 125ha site began in 2010 and was funded by a $500m investment. Two years after work commenced, the first tyres – solid units for industrial use on concrete – left the production line.
More recent Bhuj developments include a 10ha research and development site, completed in 2017. Among other areas, this includes laboratories for testing carcase and tread designs, and compound formulations and blends. Four simulators allow loads and impacts in different situations to be simulated before concepts are selected for further development.
Physical testing includes tyre rollers/rotators, which operate up to 24 hours a day for as long as 120 hours at a time, producing rotational wear and side load stresses to allow impacts to be assessed. Meanwhile, there are also the Indian agricultural tyre industry’s only ‘real world’ external test tracks, including a long tarmac facility to assess wear characteristics and noise; a tarmac, mud, and stone combination to test durability; and an automated track where tractors can be installed and run driverless to simulate and assess the long-term effects of steering and turning.
Manufacturing on the Bhuj site includes a new radial tyre production facility completed in 2021, boosting company production to 700 tonnes of radial tyres daily, of which the new Bhuj plant represents 436 tonnes. The company manufactures its own tyre moulds, and the use of technology is extensive to maximise the quality of products and working conditions, with robots cutting raw material rubber sheeting to size, and cameras checking production process quality.
Some 40-45 export containers leave the site each day, with tyres drawn from a finished product storage facility that covers 5ha (12.5ac) under a 260m x 190m single roof, able to hold 15 days’ production, or 82,500 tyres weighing 6500 tonnes, to ensure they are protected from weathering before despatch.
In an additional $0.5bn investment, BKT’s presence in Bhuj is now being extended in size by 30% to 323ha, in a move that will enable the firm to not only further increase tyre output but also ramp up production of carbon black, a key ingredient in tyre compounds.
The firm began production of its own carbon black in 2017, being the first tyre maker of its type to do this. BKT now manufactures around 165,000 tonnes annually, and the new operation will extend this to 200,000 tonnes. It’s anticipated the carbon black plant will be operating within two years, producing 600,000 tonnes annually by 2026.
Environmental responsibilities
BKT says it fully recognises its environmental responsibilities as a tyre manufacturer and is addressing them in multiple ways. As an example, Bhuj incorporates its own modern high-efficiency power plant, comprising two 20MW steam turbines, supported by solar panels and wind turbines that generate up to 50 per cent of the factory’s electricity requirements. Approximately 900 families live in a village constructed on-site for staff, and a school is under construction, to minimise workforce impact in an area which was previously sparsely populated.
Natural rubber remains an important tyre ingredient, and the company’s lab work is currently assessing higher levels of natural product integration into tyre manufacture, part of a wider aim to minimise plastic and oil usage. Research is also ongoing into used tyre recycling, a significant challenge given they’re a compound of rubber, synthetic materials and metals.
With the Bhuj plant alone using 4M litres daily, tyre manufacturing is a water-hungry process, and there are large areas of storage on-site for captured rainwater. All used water is treated and recycled via reservoirs on site, stocked with fish to help gauge quality. Almost a third of the site area is planted, and an on-site nursery produces bushes and trees to build on and replenish this.
OEM and replacement track markets
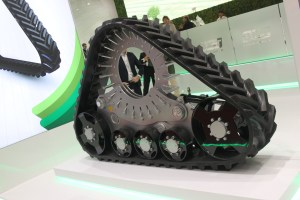
Track production at Bhuj recently began, with current production at 20-25/day of the 18x6x44 units in a pre-production/testing phase.
After building brand awareness in the agricultural tyre market over recent years, BKT has recently branched out into OEM/replacement tracked tractor rubber, with the launch last year of Agriforce BK T71 for high-hp machines.
As with most tyre/track manufacturers, BKT keeps the formula for its rubber compound closely-guarded but describes it as a ‘high performance’ formulation designed to provide strong resistance against cuts, tears and abrasion. Research into the ideal tread is reckoned to have produced an optimised pattern said to maximise traction and ride comfort, while the shape of the positive-drive lugs is claimed to maximise flexibility, and the carcase is made from four ply layers reinforced with high-tensile steel cord.
Track production at Bhuj recently began, with current production of around 20-25/day of the 18x6x44 units in a pre-production/testing phase before deals with OEMs and with suppliers for replacement sales begin. By next year the aim is to increase production 10-fold, for which a dedicated track production facility is being built.
“While track units have been developed initially for use on tractors, the next market to be targeted will be OEM and replacement combine tracks,” said Dilip Vaidya, BKT technical director. “We’re also developing new solid tyres for machine applications on concrete, taking us into other agricultural markets such as uses on compact forklifts for use in vegetable processing plants.
“And we are also working closely with the development of electrically-powered tractors, with the tyre designs necessary to make the most of their capabilities and match their specific needs, such as minimising rolling resistance to maximise battery charge life.”
This article was taken from the latest issue of CPM. For more articles like this, subscribe here.
Sign up for Crop Production Magazine’s FREE e-newsletter here.
The post A taste of India appeared first on cpm magazine.
Continue reading on CPM website...
If you are enjoying what you read then why not considering subscribing here: http://www.cpm-magazine.co.uk/subscribe/