pycoed
Member
- Location
- Pontarddulais, UK
Been using my 7045 with an old Twose back actor on it for the last month or two. When I connected it, the quick connect moved sideways quite a bit, showing that the pipe & banjo onto the top of the hydraulic cover is loose. (There is no plate locating the two Q/C s on this both just poke out at the rear) The return Q/C is quite rigid.
I noticed quite a bit of oil leakage whilst using the digger in one spot & saw the oil dripping freely down the side of the transmission roughly below the banjos.
I jibbed at removing the floor to get at these, since to do that you have to remove the back panel, on which I had mounted additional spools & Q/Cs & a linkage control lever. Removed the seat – amazingly heavy! & rubber matting, then drilled a 3” hole & used angle grinder to make a neatish slot. This gave me access to the two banjos for the external hydraulics.
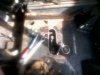
I reckoned the leak was coming from the output connector screwed into the hydraulic distributor. Oil seemed to be oozing out below the banjo where this connector is threaded into the distributor. Of course
that was directly under a C section cab crossmember, so another hole 35mm had to be drilled directly above the leaking connector carefully avoiding the legs of the C .
Banjo came off easily but the connector is F tight! Judging by the double washers on the banjo, I reckon the previous owner had trouble here, so this connector may be loctited in.
Next day:- Right - it's out! There was a load of sealer or some such above the O ring - looks like it had been bodged full of sealer to try to stop the leak. Also found the main problem was that a wrong banjo bolt had been fitted that needed multiple washers to seal at all on the pipe to the rear – sorted that in the lathe.
I then had to remove the copper washer below the connector. Again it looks like a wrong washer has been fitted & whaled down on to try to seal. but the copper has expanded & is really stuck on it's seat & all around the circumference.
Ended up having to drill the copper washer to get a pick in to remove it. Packed the oilway with shop towel & got magnetic probe at the ready. Careful as you go – the waher is only 1.5mm thick! Out it came & was only 1mm thick so I found I had drilled into the seat - two nice clean 2mm divots. About .5 mm deep AAARRGGHHH!!
Just spent the last 2 hours making a spot facer to clean up the seat. Length of 5/8” bar cross drilled & filed square to take a 1/4”SQ HSS cutter. End drilled for a grub screw. Nylon pilot turned & fitted to the shaft & end turned down to fit in drill on low low speed. I am glad to say it was successful clean as a baby’s bum & no sign of chatter.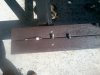
Left to right is the spot facer, shortened banjo bolt & the connector that the banjo screws into.
Lovely working on 40 year old, multiple owner kit – two 4 hour days just to clear up an oil leak!
I noticed quite a bit of oil leakage whilst using the digger in one spot & saw the oil dripping freely down the side of the transmission roughly below the banjos.
I jibbed at removing the floor to get at these, since to do that you have to remove the back panel, on which I had mounted additional spools & Q/Cs & a linkage control lever. Removed the seat – amazingly heavy! & rubber matting, then drilled a 3” hole & used angle grinder to make a neatish slot. This gave me access to the two banjos for the external hydraulics.
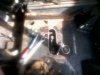
I reckoned the leak was coming from the output connector screwed into the hydraulic distributor. Oil seemed to be oozing out below the banjo where this connector is threaded into the distributor. Of course
Banjo came off easily but the connector is F tight! Judging by the double washers on the banjo, I reckon the previous owner had trouble here, so this connector may be loctited in.
Next day:- Right - it's out! There was a load of sealer or some such above the O ring - looks like it had been bodged full of sealer to try to stop the leak. Also found the main problem was that a wrong banjo bolt had been fitted that needed multiple washers to seal at all on the pipe to the rear – sorted that in the lathe.
I then had to remove the copper washer below the connector. Again it looks like a wrong washer has been fitted & whaled down on to try to seal. but the copper has expanded & is really stuck on it's seat & all around the circumference.
Ended up having to drill the copper washer to get a pick in to remove it. Packed the oilway with shop towel & got magnetic probe at the ready. Careful as you go – the waher is only 1.5mm thick! Out it came & was only 1mm thick so I found I had drilled into the seat - two nice clean 2mm divots. About .5 mm deep AAARRGGHHH!!
Just spent the last 2 hours making a spot facer to clean up the seat. Length of 5/8” bar cross drilled & filed square to take a 1/4”SQ HSS cutter. End drilled for a grub screw. Nylon pilot turned & fitted to the shaft & end turned down to fit in drill on low low speed. I am glad to say it was successful clean as a baby’s bum & no sign of chatter.
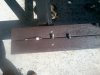
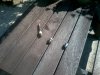
Lovely working on 40 year old, multiple owner kit – two 4 hour days just to clear up an oil leak!