Written by Justin Roberts from Agriland
Mineral-oil-based fuels suffer a good deal of bad publicity, but the government’s enthusiasm for batteries as a universal method of energy storage means that alternative sources of diesel are overlooked.
Carbon-based fuels, such as diesel, have several advantages over lithium-ion cells – the major one being that they contain around four times as much energy than batteries on a volumetric basis.
Another benefit of a liquid fuel includes the ease of handling and an existing infrastructure dedicated to its distribution.
All of Ireland’s commercial, and most of its personal transport, also run on carbon-based fuels, meaning engines are becoming ever cleaner and more efficient to run.
With these advantages still very much relevant, exploring other non-fossil sources for carbon fuels would appear a sensible solution and indeed, there is a growing interest in doing so with plans afoot to increase their availability.
Carbon is nature’s answer to energy management. It is found in all living tissue, along with hydrogen (H), as the basic building block of life.
This ubiquity suggests that if it were possible to recover it from organic waste to create a diesel substitute, then it may distributed via the present fuelling infrastructure, rather than rip it all out and start again with electrical charging points, a project that will be both hugely expensive and disruptive.
And it is indeed possible with two distinct approaches to doing so, the Fischer–Tropsch process and pyrolysis.
Pyrolysis is taking organic matter to high temperatures in the absence of oxygen, resulting in the production of hydrocarbons in the form of gasses such as hydrogen and liquids, and ranging from turpentine to tar.
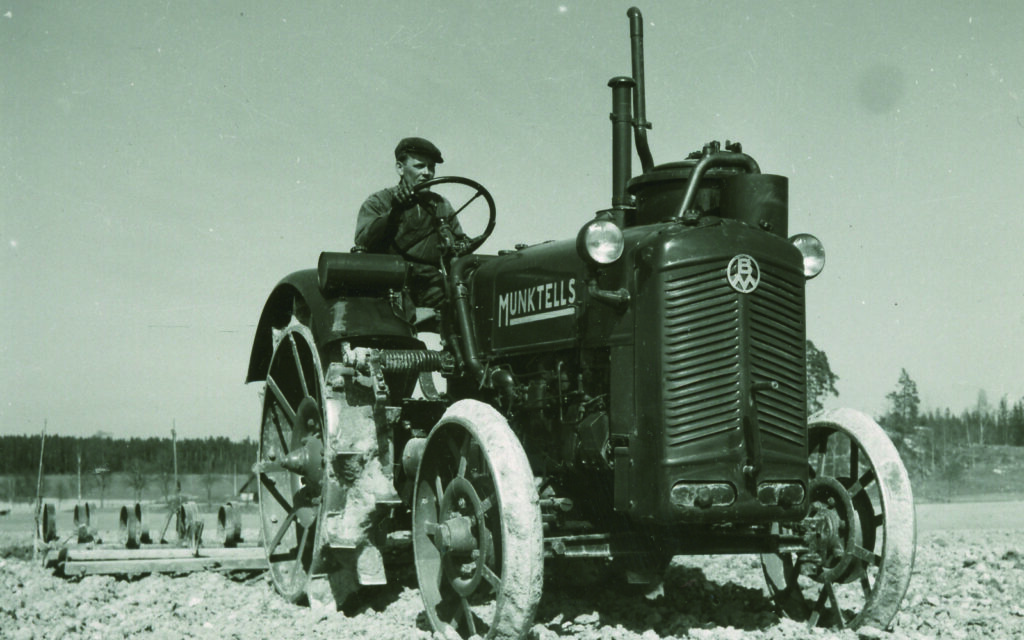
Wood gas is a form of pyrolysis and was common during both the World Wars
It is the process behind the wood-gas producer tractors of the two World Wars, and if it is skewed towards maximising gas production in this way, it is often referred to as gasification.
The resulting products are a mix of hydrogen and carbon monoxide as the gas fraction, and tar, which can be refined to produce a diesel substitute directly, or it can all be used as feedstock for the Fischer-Tropsch process.
Pyrolysis is the process normally associated with the extraction of fuel from tyres with the average worn car tyre yielding around 2L of diesel.
Tyre dumps are not an inexhaustible energy source, but with 1.5 billion of them being dumped annually worldwide, there is plenty of scope for recovering some energy as well as dealing with a waste disposal issue.
It is the Fischer-Tropsch process which lies at the heart of the diesel synthesis. It was developed in Germany in 1925 to create synthetic fuel and other oils from the country’s plentiful coal reserves.
Being nearly a century old, the process is well understood.
It can utilise natural gas and biomass as feedstocks to produce synthetic diesel. It is this that lies behind the promotion of gas to liquid (GTL) and hydrogenated vegetable oil (HVO) as an alternative to fossil fuels.
Other advantages of the Fischer-Tropsch method is that it requires relatively low temperatures and pressures to work.
The metallic catalysts used are also cheap, iron and nickel being two of the several that can be used.
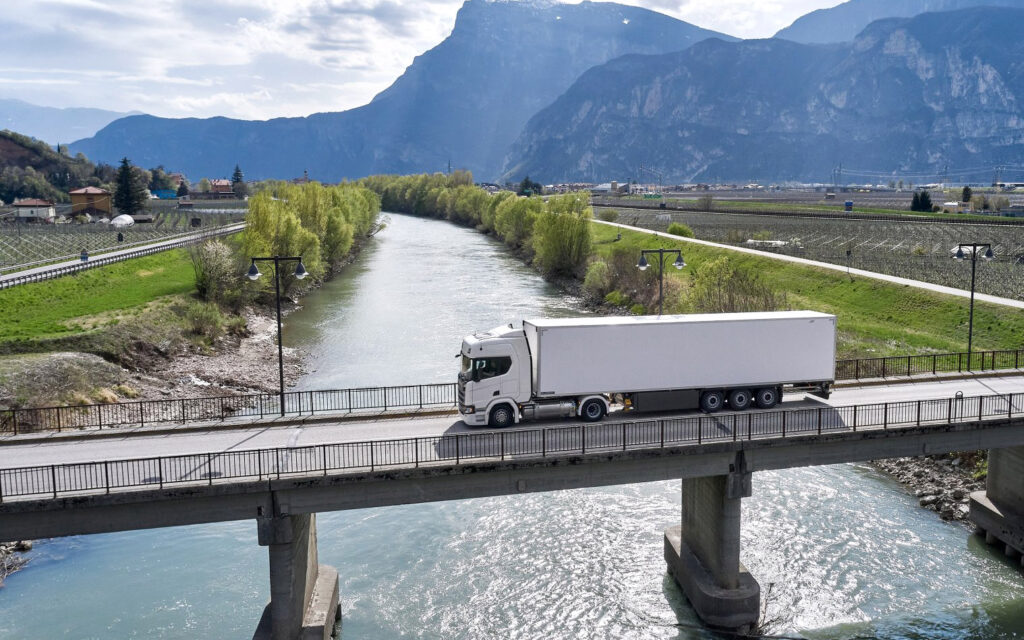
Truck manufacturers such as Scania are also exploring all the options and it is the haulage industry which is likely to drive HVO availability
By adjusting all these factors, the relative yield of the hydrocarbons formed can be fine tuned to ensure that a drop in replacement for mineral-derived diesel is produced.
Because there is no need for extreme conditions in the production process, the necessary reaction vessels and other items of hardware can be small and low in cost, compared to what might be found in a standard oil refinery, enabling plants to be built on a local scale.
This opens the prospect of farmers or co-ops building and running their own, using organic material already found on the farm, or grown specifically for fuel production.
Methane collected from slurry stores can also be used as a feedstock.
The post Machinery: Ramping up diesel production from biomass appeared first on Agriland.co.uk.
Continue reading on the Agriland Website...
Mineral-oil-based fuels suffer a good deal of bad publicity, but the government’s enthusiasm for batteries as a universal method of energy storage means that alternative sources of diesel are overlooked.
Carbon-based fuels, such as diesel, have several advantages over lithium-ion cells – the major one being that they contain around four times as much energy than batteries on a volumetric basis.
Another benefit of a liquid fuel includes the ease of handling and an existing infrastructure dedicated to its distribution.
All of Ireland’s commercial, and most of its personal transport, also run on carbon-based fuels, meaning engines are becoming ever cleaner and more efficient to run.
With these advantages still very much relevant, exploring other non-fossil sources for carbon fuels would appear a sensible solution and indeed, there is a growing interest in doing so with plans afoot to increase their availability.
The utility of carbon
Carbon is nature’s answer to energy management. It is found in all living tissue, along with hydrogen (H), as the basic building block of life.
This ubiquity suggests that if it were possible to recover it from organic waste to create a diesel substitute, then it may distributed via the present fuelling infrastructure, rather than rip it all out and start again with electrical charging points, a project that will be both hugely expensive and disruptive.
And it is indeed possible with two distinct approaches to doing so, the Fischer–Tropsch process and pyrolysis.
Pyrolysis is taking organic matter to high temperatures in the absence of oxygen, resulting in the production of hydrocarbons in the form of gasses such as hydrogen and liquids, and ranging from turpentine to tar.
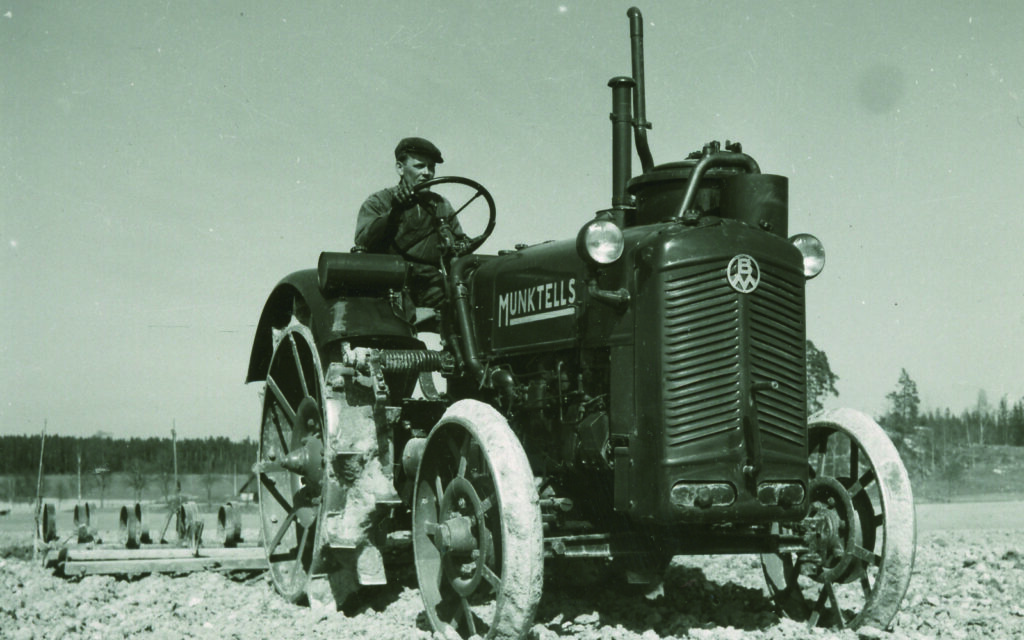
Wood gas is a form of pyrolysis and was common during both the World Wars
It is the process behind the wood-gas producer tractors of the two World Wars, and if it is skewed towards maximising gas production in this way, it is often referred to as gasification.
The resulting products are a mix of hydrogen and carbon monoxide as the gas fraction, and tar, which can be refined to produce a diesel substitute directly, or it can all be used as feedstock for the Fischer-Tropsch process.
Pyrolysis is the process normally associated with the extraction of fuel from tyres with the average worn car tyre yielding around 2L of diesel.
Tyre dumps are not an inexhaustible energy source, but with 1.5 billion of them being dumped annually worldwide, there is plenty of scope for recovering some energy as well as dealing with a waste disposal issue.
Diesel fuel synthesis
It is the Fischer-Tropsch process which lies at the heart of the diesel synthesis. It was developed in Germany in 1925 to create synthetic fuel and other oils from the country’s plentiful coal reserves.
Being nearly a century old, the process is well understood.
It can utilise natural gas and biomass as feedstocks to produce synthetic diesel. It is this that lies behind the promotion of gas to liquid (GTL) and hydrogenated vegetable oil (HVO) as an alternative to fossil fuels.
Other advantages of the Fischer-Tropsch method is that it requires relatively low temperatures and pressures to work.
The metallic catalysts used are also cheap, iron and nickel being two of the several that can be used.
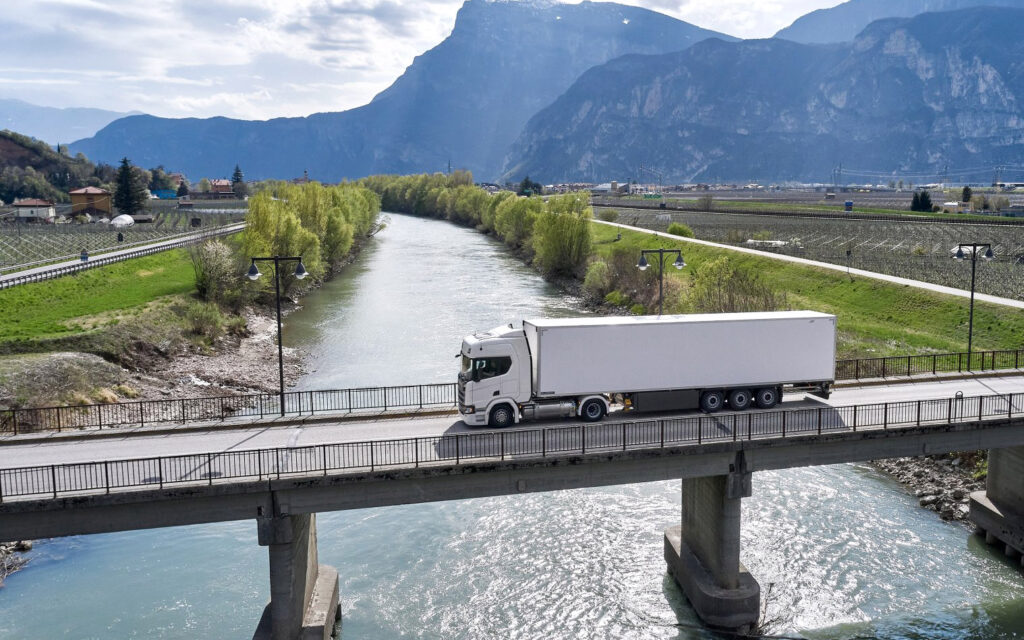
Truck manufacturers such as Scania are also exploring all the options and it is the haulage industry which is likely to drive HVO availability
By adjusting all these factors, the relative yield of the hydrocarbons formed can be fine tuned to ensure that a drop in replacement for mineral-derived diesel is produced.
Because there is no need for extreme conditions in the production process, the necessary reaction vessels and other items of hardware can be small and low in cost, compared to what might be found in a standard oil refinery, enabling plants to be built on a local scale.
This opens the prospect of farmers or co-ops building and running their own, using organic material already found on the farm, or grown specifically for fuel production.
Methane collected from slurry stores can also be used as a feedstock.
The post Machinery: Ramping up diesel production from biomass appeared first on Agriland.co.uk.
Continue reading on the Agriland Website...